coppley Clothing Plant
hamilton, ONTARIO
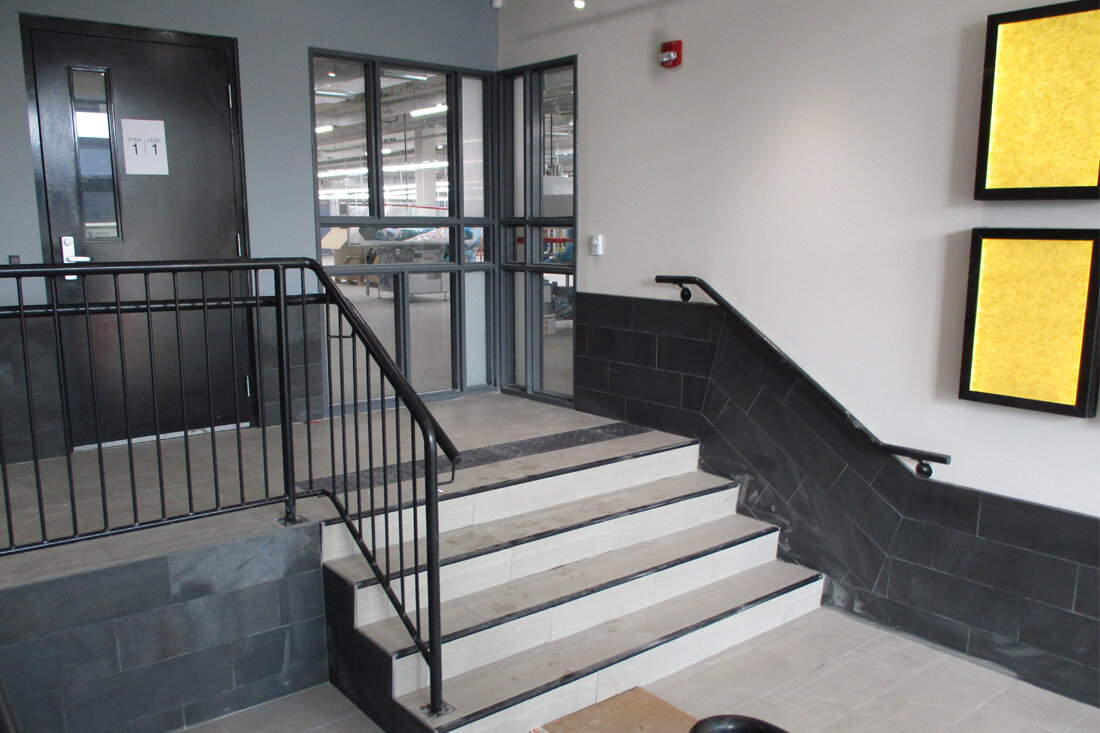
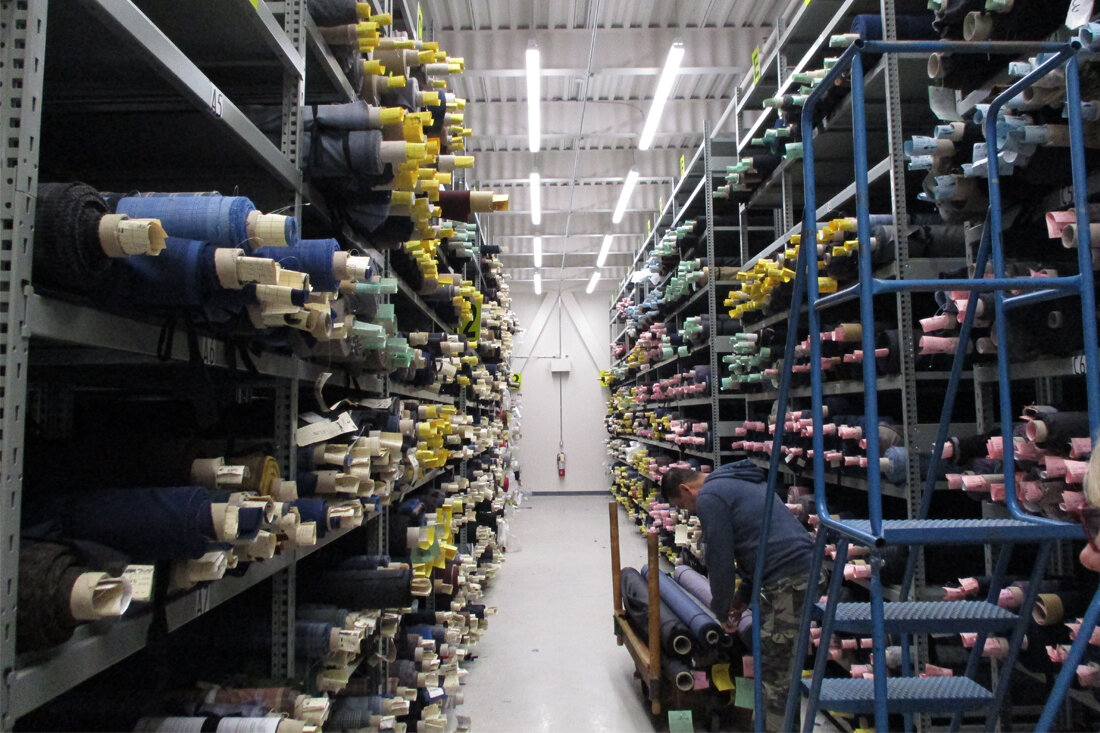
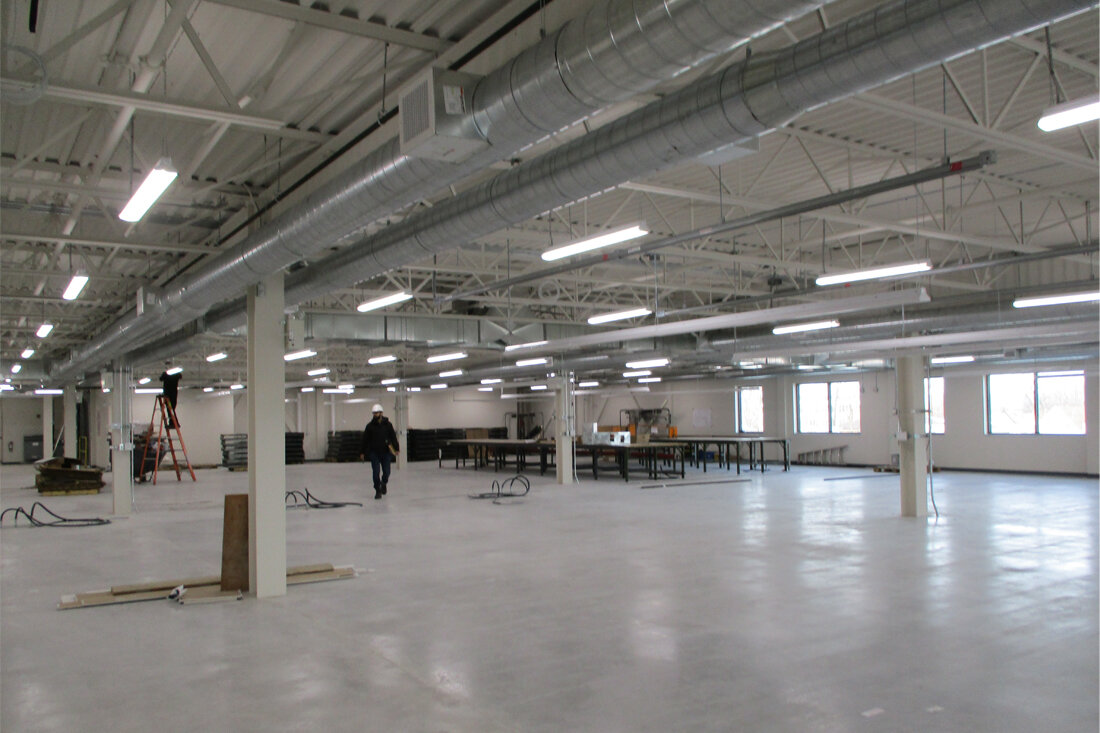
Client Coppley Ltd.
Size 70,000 sq. ft. (6,503 sq. m.)
With over 135 years history in Hamilton, renowned menswear maker Coppley Ltd., moved from three separate buildings to a new manufacturing facility in a 70,000-square-foot, three-storey building that consolidates the company's operations and 270 staff under one roof.
The shell was delivered as a design/build/lease-to-own contract, and CGS advised Coppley in defining their space requirements, on site selection, plant requirements and lease specifications, guided the shell design, and assisted in Landlord negotiations. The Tenant improvements were delivered as a traditional design/bid/build contract.
The tight site is on the edge of downtown providing safe and easy access for their largely immigrant, female staff who need public transit and often work evening shifts. A one storey plant would have been more ideal but impossible downtown. The resulting multi-storey solution required automated garment hoists, a large elevator and exterior doors for equipment hoisting to each floor.
The decision by the company to stay in Hamilton is important since so much garment manufacturing has gone offshore, but Coppley have thrived in the American market even while facing its greatest test ever with the movement to casual dressing. They revolutionized the tailored clothing industry's way of doing business by delivering made-to-measure suits within seven days. To do this the company has built up a key asset in a skilled workforce, but their spaces were old, inefficient and inadequate. Coppley now has provided employees with high quality workspaces in a comfortable, modern and consolidated building where staff work together more collaboratively and efficiently.
Coppley’s very diverse workforce mix rare old world tailoring skills and state of the art computer cutting. They require well-lit workstations for visual acuity, a stable environment for cloth, and an array of process vacuum, steam, power, data and compressed air to workstations. Efficient production flow drove the design, but human factors like daylight and view, easy refreshment and washroom access were critical also. Daylighting is critical to the sewing and colour match work, so an LED daylighting-colour system with perimeter zone shedding is used throughout, as well as generous windows around all the production areas.
A central cafeteria on the mid floor with multiple entrances and food prep stations, and varied seating accommodates peak occupant loads of about 100 staff at a time, and helps build community. It is designed with bright colours and durable, high quality finishes and sound masking since breaks are busy and loud, but important for comfort and relaxation from demanding work.
CGS authored the concept for the plant on the selected site. Existing building elements were maintained where possible integrated with a new flexible three storey production floor. Support spaces are positioned out of the way of production flow with modularity for repetition from floor to floor ensuring legibility and economy. Production offices have glazed fronts and bright colours to help animate the production floor areas.
A varied palette of bright paint colours add simple, inexpensive warmth and visual interest to the busy, intense workplace.
Loading and service spaces are tightly grouped for efficiency in a corner of the site with truck access from an arterial street flanking the site, with the front entrance addressing a quieter side street and visitor parking on the street.
The modest entrance lobby includes brand display elements, and leads to a small but carefully designed showroom and sales areas for customer visits.